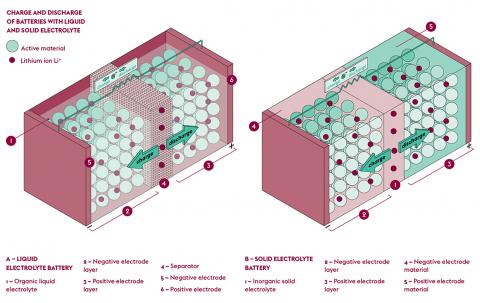
Charging tomorrow’s electrochemical cell - L'Edition #12
(Article from L'Edition N°12 - march 2020)
Lithium-ion, sodium-ion, magnesium-ion and all-solidstate batteries: Université Paris- Saclay researchers are thinking up new energy storage and conversion systems that offer better autonomy and longevity.
Last October, the Swedish Academy awarded the 2019 Nobel Prize in Chemistry to the inventors of the lithium-ion battery, thus recognising one of the greatest technological advances of the 20th century. A long way from the initial trial and errors of the 70s, today’s rechargeable battery has applications that have revolutionised energy storage and production methods, and secured it a place of prominence in the markets of portable electronics and electric automobiles.
Its operating principle is based on the flow of lithium ions between two solid electrodes thanks to chemical reactions, resulting in conversion of chemical energy into electrical energy. Present in an electrolyte (a mixture of organic solvents and dissolved salts), lithium ions (Li+) follow a reversible flow from one electrode to another depending on charge/ discharge cycles. The positive electrode (cathode), currently made of lithium-cobalt oxide, and the negative electrode (anode), typically made of graphite, exchange their lithium ions during a complete cycle.
“The biggest advantage of lithium-ion batteries is their great energy density per unit of mass and volume,” says Sylvain Franger of the Orsay Institute of Molecular and Material chemistry (ICMMO – Université Paris-Saclay, CNRS). The main challenges of current research on the electrode materials as well as the electrolyte, focus on further increasing storage capacity, improving the battery lifecycle to withstand charge/discharge cycles, and enhancing security. “However, optimisation of all criteria is still very tricky.”
Offsetting battery ageing
At ICMMO, Franger dedicates his time to understanding the inner workings of commercial lithium-ion batteries, be they in use or at rest. With his team, he tests and models battery ageing to identify determining parameters, such as temperature, charging/discharging regimes, the charge state and the depth of discharge.
There are several aspects to the complex ageing process. “Like human beings, the materials are naturally worn out over the course of their use. Their crystallographic structure is deformed, and they lose their original properties. Lithium is trapped in certain sites and becomes inaccessible. Now, each time lithium is lost or prevented from working, capacity for the system dwindles”, says Franger. Other phenomena cause volume expansion in the materials over the course of charge/discharge cycles. “These ’respirations’ have consequences on the overall cohesion of the electrode.”
To maintain good performance in batteries, the stability of the electrode and electrolyte is essential. “During ageing, the electrolyte solvents decompose in the interphase between the electrolyte (liquid) and the surface of the electrode (solid), to form decomposition products (sometimes gaseous), potentially flammable, corrosive and toxic. The solid products are deposited at the surface of the electrode and grow unchecked, forming a layer called the Solid Electrolyte Interphase or SEI,” explains Franger. “By consuming matter, the SEI changes the kinetic properties of the battery and triggers parasitic reactions. In extreme cases, such as rapid recharge, thermal runaway occurs and the battery can catch fire.” The dilemma? This layer is also necessary because it protects the system by passivating the electrodes and impeding the continuous decomposition of the electrolyte. The challenge is to achieve its optimisation.
An accelerated model of ageing thanks to radiolysis
In the Interdisciplinary Laboratory on Nanoscale and Supramolecular Organisation (LIONS) of the Nanoscience and Innovation for Materials, Biomedicine and Energy unit (NIMBE – Université Paris-Saclay, CNRS, CEA), Sophie Le Caer uses radiation chemistry (β- and γ) to trigger the accelerated ageing of matter, enabling her to test different mixtures of electrolytes and electrode materials, in order to better understand the SEI. The researcher examines the nature and quantity of the decomposition products obtained in gaseous and liquid form. “The decomposition is very fast, and in minutes or hours the same molecules are obtained qualitatively – just in different proportions – as in cycling ageing tests, which are slower.” These results lay the groundwork for screening tests. “In addition, thanks to pulse radiolysis – a time-resolved technique – we are able to determine speed constants associated with certain chemical reactions.”
Recently, Sophie Le Caer and Sylvain Franger worked together to test carbon nanoparticles suspended in an electrolyte and subjected to irradiation. “We’ve seen the emergence of patches of decomposition products, which were then analysed by X-ray photoelectron spectroscopy (XPS). The oxalates and lithium carbonates identified are typically decomposition products observed in Li-ion batteries.” These results demonstrate the usefulness of the properties of materials modified by radiolysis in the study of batteries.
Emerging and promising Technologies
While the Li-ion technology still has a bright future, other types of rechargeable electrochemical batteries are creeping into the picture. “The locations of the world’s reserves of lithium and other widely used metals such as cobalt, are problematic in terms of supply and exploitation,” says Franger. “It is important to control or even reduce their use, to make these systems ecologically-compatible throughout the production process, from ore extraction to recycling.”
At the Laboratory for the Study of Light Elements (LEEL) of NIMBE, Magali Gauthier is interested in a still very recent technology: magnesium ion (Mg-ion) batteries. Magnesium is widely abundant on Earth and is also very affordable. “One of the biggest advantages of magnesium ion (Mg2+) lies in its capacity to exchange two electrons,” says the researcher. “In theory, the power capacity of Mg-ion batteries could be double that of Li-ion. But because the magnesium ion interacts more strongly with its environment, its mobility and material reactivity are modified. Electrolytes analogous to those used in the Li-ion batteries don’t work here and the passivation layer doesn’t allow the ions to pass.”
To improve the system, the researcher studies different anode alloys and their compatibility with the electrolytes. Recently, she tried a micrometric alloy of indium and antimony obtained by grinding. “The theoretical capacity of antimony is very high, but alone, the metal irreversibly traps magnesium ions in its structure: the battery therefore is not rechargeable. By combining it with indium in the form of an alloy, we can partially unblock the reaction and around forty charge/discharge cycles become possible.” During the reactions, the researcher has also observed some transformation of certain alloying phases into crystals or amorphous solids. “We are currently trying to better understand this phenomenon and the reactivity of the alloy, and evaluate performance as a result.”
The first sodium all-solid-state Battery
As for Sylvain Franger, he is keen on all-solidstate batteries, i.e. with an electrolyte that is solid instead of liquid. One of its advantages is that it does not allow the development of dendrites that otherwise appear during rapid recharge. These growing, uneven deposits of metal at the surface of the electrode create short circuits when they reach the other electrode. “However, because the solid electrolytes are polycrystalline, they manage to make their way through the juncture of the grains that are softer, and the porosity of the ceramic.”
Because it is drastically compact, the all-solidstate battery also promises unprecedented levels of power capacity per unit volume. “In addition to being more secure, it doesn’t contain flammable elements and being solventfree means that it does not leak. It is also much easier to recycle,” says Franger.
For the past two years, his team, in partnership with Greenfish company, has set a twofold challenge: to develop an all-solid sodium battery to combine the advantages of both systems. Like magnesium, sodium is very abundant on Earth and ubiquitously distributed. “But the sodium atom is larger and heavier than that of lithium and it has a different mobility. This means we need to go back on chemistry and materials,” points out Sylvain Franger.
Pioneers in the field, he and his team are determined to overcome technological obstacles in the system. They are interested in glass or ceramic solid electrolytes of the oxide family, seeking to improve the mechanical properties and increase ionic conductivity by changing the chemistry of the composition. “We have since demonstrated the concept’s legitimacy thanks to our materials.” The battery (of the future?) is charging and loading!
Publications
∙ Sylvain Franger et al., Combining a Fatigue Model and an Incremental Capacity Analysis on a Commercial NMC/Graphite Cell under Constant Current Cycling with and without Calendar Aging. Batteries 2019, 5, 36.
∙ Magali Gauthier et al., Unexpected Behavior of the InSb Alloy in Mg-Ion Batteries: Unlocking the Reversibility of Sb. J. Phys. Chem. C 2019, 123, 1120−1126.
∙ Sophie Le Caer et al., Ex situ solid electrolyte interphase synthesis via radiolysis of Li-ion battery anode–electrolyte system for improved coulombic efficiency. Sustainable Energy Fuels 2 (2018) 2100.