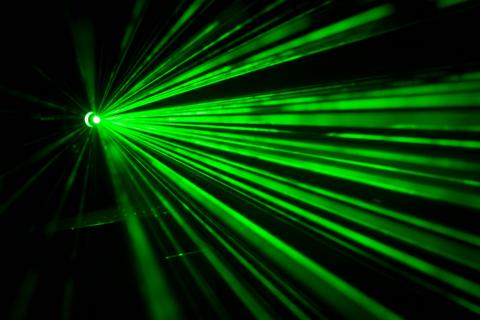
L’effet laser en régime continu démontré à partir d’un alliage de germanium-étain
Des chercheurs du Centre de nanosciences et de nanotechnologies (C2N - Université Paris-Saclay, CNRS) ont mis au point une nouvelle méthode d’ingénierie du matériau pour fabriquer un microdisque laser en alliage de germanium-étain (GeSn), en collaboration avec des chercheurs du Centre de recherche de Jülich en Allemagne, et de la société franco-italienne STMicroelectronics. Cette méthode permet pour la première fois d’observer un effet laser continu avec des composés semi-conducteurs du groupe IV et dont la puissance nécessaire pour son fonctionnement est très inférieure à celles utilisées jusqu’à présent.
Les limites du procédé actuel
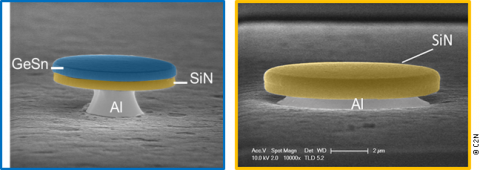
Clichés en microscopie électronique du microdisque composé de couches de GeSn et SiNx déposé sur une couche d'aluminium. A droite, la structure en microdisque après un dernier dépôt de SiN. Crédits : C2N / M. El Kurdi & al.